FMEA and FMECA Services
At SILS Enterprise, we provide comprehensive Failure Mode and Effects Analysis (FMEA) and Failure Mode, Effects, and Criticality Analysis (FMECA) services. Our expertise ensures your products and systems are reliable, safe, and meet the highest standards of quality.
FMEA/FMECA
What is FMEA?
Failure Mode and Effects Analysis (FMEA) is a systematic method for identifying potential failure modes in a product or process and analyzing the effects of these failures. FMEA helps prioritize risks and implement corrective actions to improve reliability and prevent failures.
What is FMECA?
Failure Mode, Effects, and Criticality Analysis (FMECA) is an extension of FMEA that includes a criticality analysis. This analysis assesses the severity, occurrence, and detectability of potential failures, providing a more detailed evaluation of risk and guiding more focused mitigation efforts.
Why Choose FMEA and FMECA?
Risk Mitigation
Identify and address potential failure modes before they occur, reducing the risk of failures.
Improved Reliability
Enhance the reliability and durability of your products by addressing weak points in design and process.
Cost Savings
Prevent costly recalls and repairs by identifying and mitigating risks early in the development process.
Regulatory Compliance
Meet industry standards and regulatory requirements for safety and quality.
Our Services
FMEA Development
We conduct thorough FMEA to identify potential failure modes and their effects on your products or processes. Our services include:
- Design FMEA (DFMEA)
- Process FMEA (PFMEA)
- System FMEA
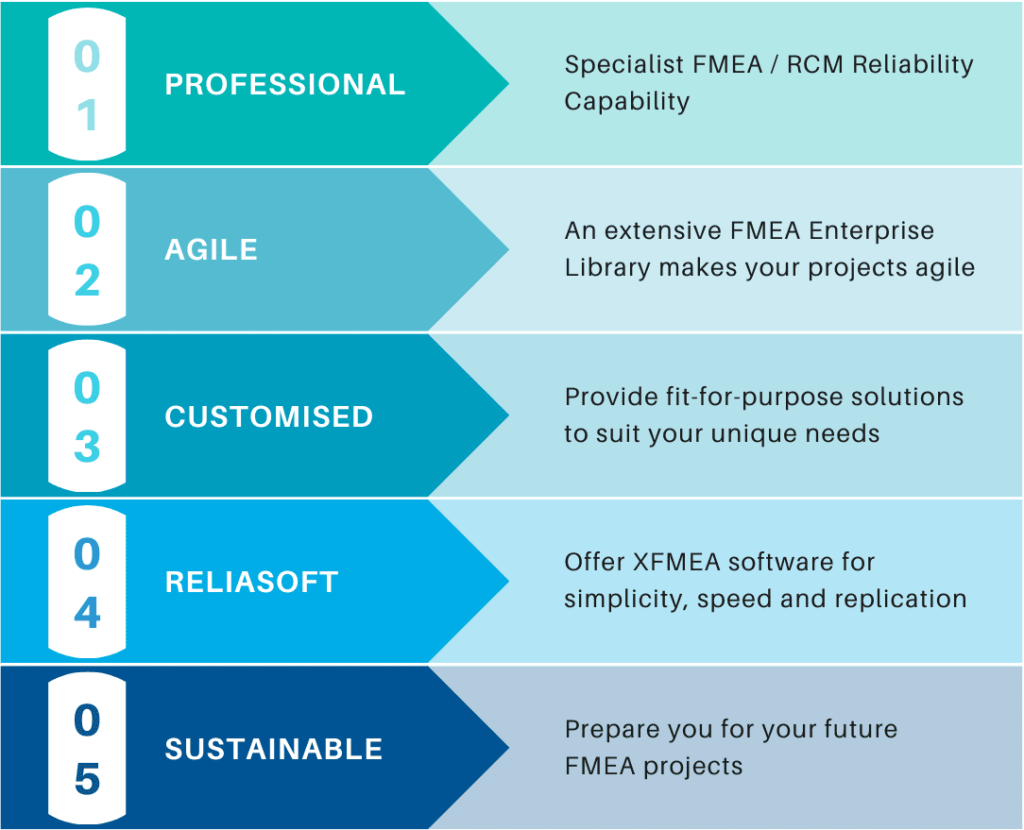
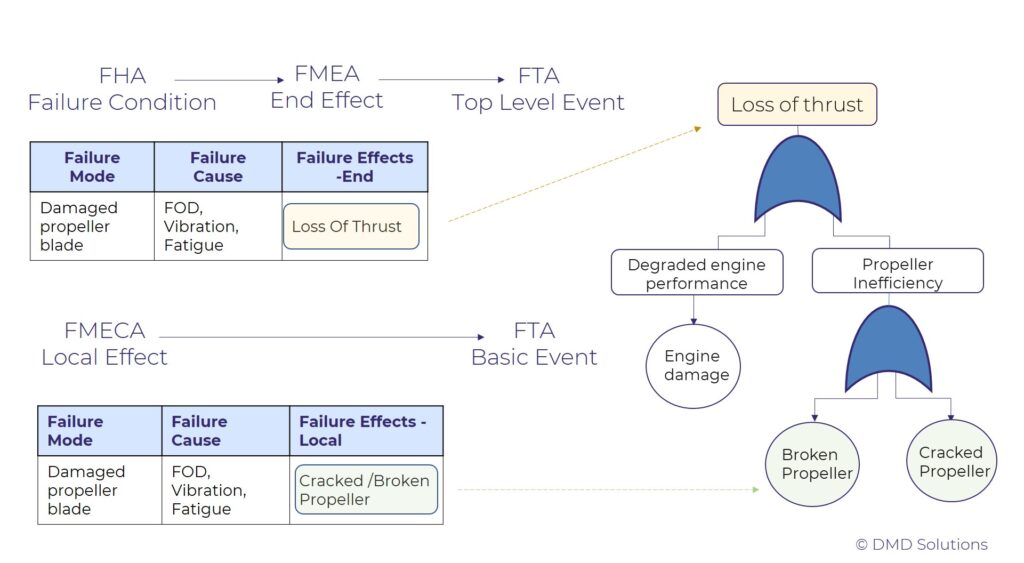
FMECA Development
We extend the FMEA process to include criticality analysis, providing a more detailed risk assessment. Services include:
- Criticality Assessment
- Severity, Occurrence, and Detectability Analysis
- Risk Priority Number (RPN) Calculation
Corrective Action Planning
We develop and implement corrective action plans based on FMEA and FMECA findings to mitigate identified risks. Key services include:
- Action Plan Development
- Implementation Support
- Effectiveness Verification
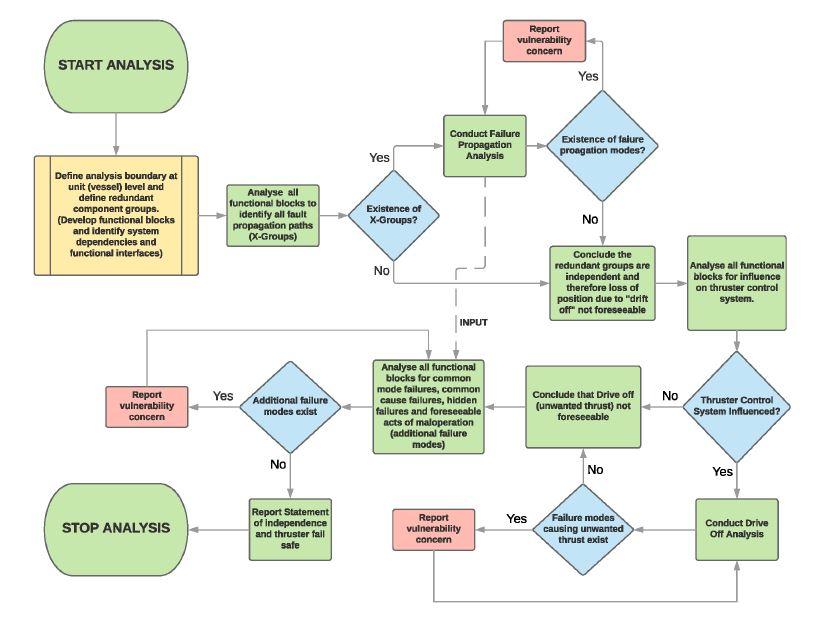
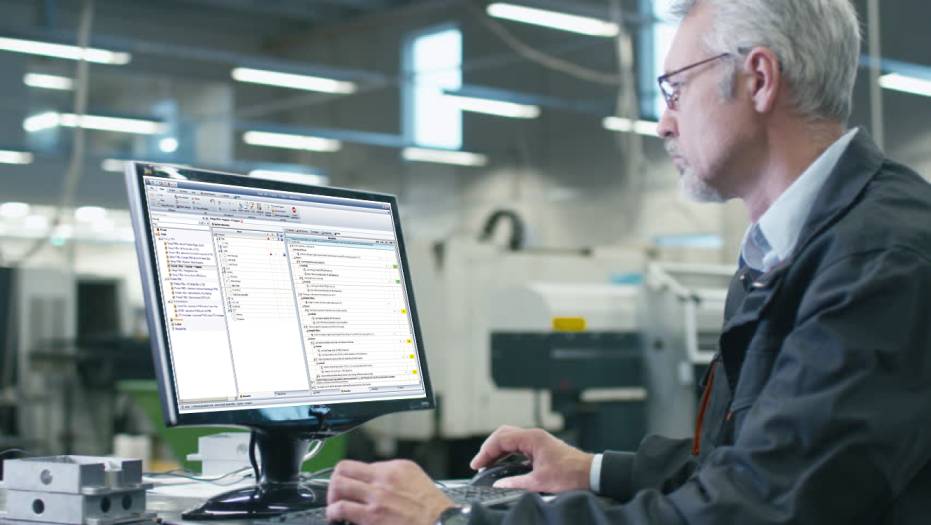
Training and Workshops
We offer training programs and workshops to help your team understand and apply FMEA and FMECA methodologies effectively. Services include:
- Customized Training Programs
- Hands-On Workshops
- Ongoing Support and Coaching
Documentation and Reporting
We provide detailed documentation and reporting to ensure transparency and traceability of the FMEA and FMECA processes. Key services include:
- Comprehensive Reports
- Documentation of Findings and Actions
- Regular Updates and Reviews
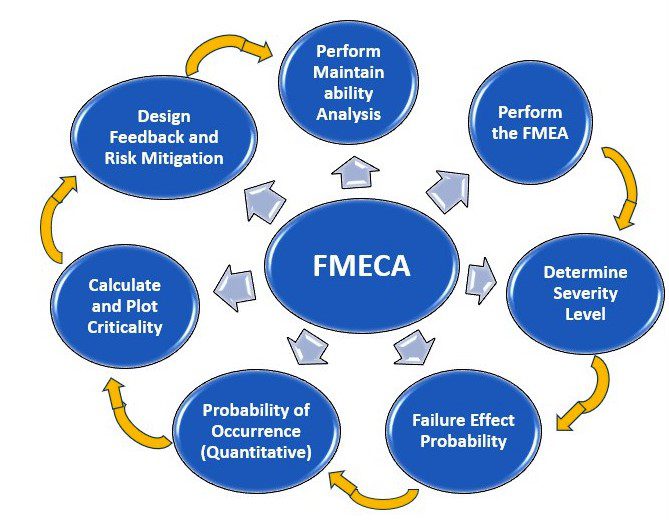
Standards We Follow
Our FMEA and FMECA services adhere to recognized international
standards to ensure the highest quality and reliability:
standards to ensure the highest quality and reliability:
ISO 9001
Quality management systems
ISO 31000
Risk management – Principles and guidelines
IEC 60812
Analysis techniques for system reliability – Procedure for failure mode and effects analysis (FMEA)
SAE J1739
Potential Failure Mode and Effects Analysis in Design (Design FMEA), Potential Failure Mode and Effects Analysis in Manufacturing and Assembly Processes (Process FMEA)
MIL-STD-1629A
Procedures for Performing a Failure Mode, Effects, and Criticality Analysis

Benefits of Our FMEA and FMECA Services
Enhanced Product Quality
Systematic analysis and mitigation of potential failures lead to higher product quality.
Increased Customer Satisfaction
Reliable and safe products result in higher customer satisfaction and loyalty.
Regulatory Compliance
Ensure compliance with industry standards and regulatory requirements.
Informed Decision-Making
Detailed risk assessments provide valuable insights for informed decision-making.
Industries We Serve
Our FMEA and FMECA services are applicable across various industries, including:
Aerospace & Defense
Ensure the reliability and safety of critical systems.
Automotive
Improve vehicle safety and performance through comprehensive risk analysis.
Healthcare
Enhance the safety and reliability of medical devices and equipment.
Manufacturing
Optimize processes and prevent failures in production systems.
Energy
Ensure the reliability and safety of energy production and distribution systems.